EPDM: a record product
EPDM is an acronym for:
Ethylene
Propylene
Diene
M-class
EPDM rubber is a terpolymer of the three monomers: ethylene, propylene and a diene-component.
EPDM rubber is the main material of the polymeric geomembranes of low permeability, manufactured by Firestone Building Inc. for over 40 years.
A chemical structure to indicate so:
The EPDM rubber, once released by the industrial production is an ELASTOMER, that is a thermosetting, a product that once vulcanized (cooked over 180 ° C) is ready to be used. (see below)
The final elasticity is due to the cross-links between different polymer chains that give a memory to the product. In practice, they promote the elastic deformation, "forcing" the chains to return to the state before deformation.
From Wikipedia (italian site)
The generic term of elastomer indicates the natural or synthetic substances which have the chemical and physical properties typical of the caucciù (or natural rubber); its most distinctive feature is the ability to endure large elastic deformations: for example, it can be stretched different times taking its size again once recreated a situation of rest.
The elastomers are molded into the desired shape by extrusion or hot forging.
The elastomers are part of the polymers and are divided into two main classes:
• thermoplastic elastomers
• thermoset elastomers
....
The thermoset elastomers are produced by linking to each other the polymer chains through the use of chemical reagents, temperature and pressure in a process generally called vulcanization. This change in structure imply the appearance of the thermosetting properties: it is impossible to remodel them once the vulcanization has occurred.
Deformation process of an elastomer. (A) is an unstressed polymer; (B) is the same polymer under stress. When the stress is removed, it will return to the A configuration. (The dots represent cross-links).
Initially, it is a product that comes from the chemical industry in the form of white little balls; thanks to the contribution of other products (each of which introduces the characteristics of the final product), it becomes a waterproof sheet.
Here a semplification of the production process, with the additives useful to create the final product with its qualifying characteristics:
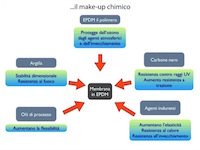
The final characteristics of the product are:
Superior physical properties
Resistance to aging and UV rays
High flexibility at low temperatures
Dimensional stability
Easy to install.
The final sizes of EPDM membranes are determined by the dimensions of industrial machineries.
The biggest membrane is 15,25 x 61 mt, otherwise, the smallest one has dimensions of 4,27 x 30,50 mt.
The Firestone EPDM membranes are commercialized with two different thikness:
- 1,02 mm (1,25 Kg/mq)
- 1,14 mm (1,41 Kg/mq)
The membrane can be jointed thanks to double-side tapes, and it can be installed in very extreme conditions of temperature: ranging from -30° C (like Siberia) to 40° C (Arab countries).
Details for the correct installation of the membrane are present in the documentary section.